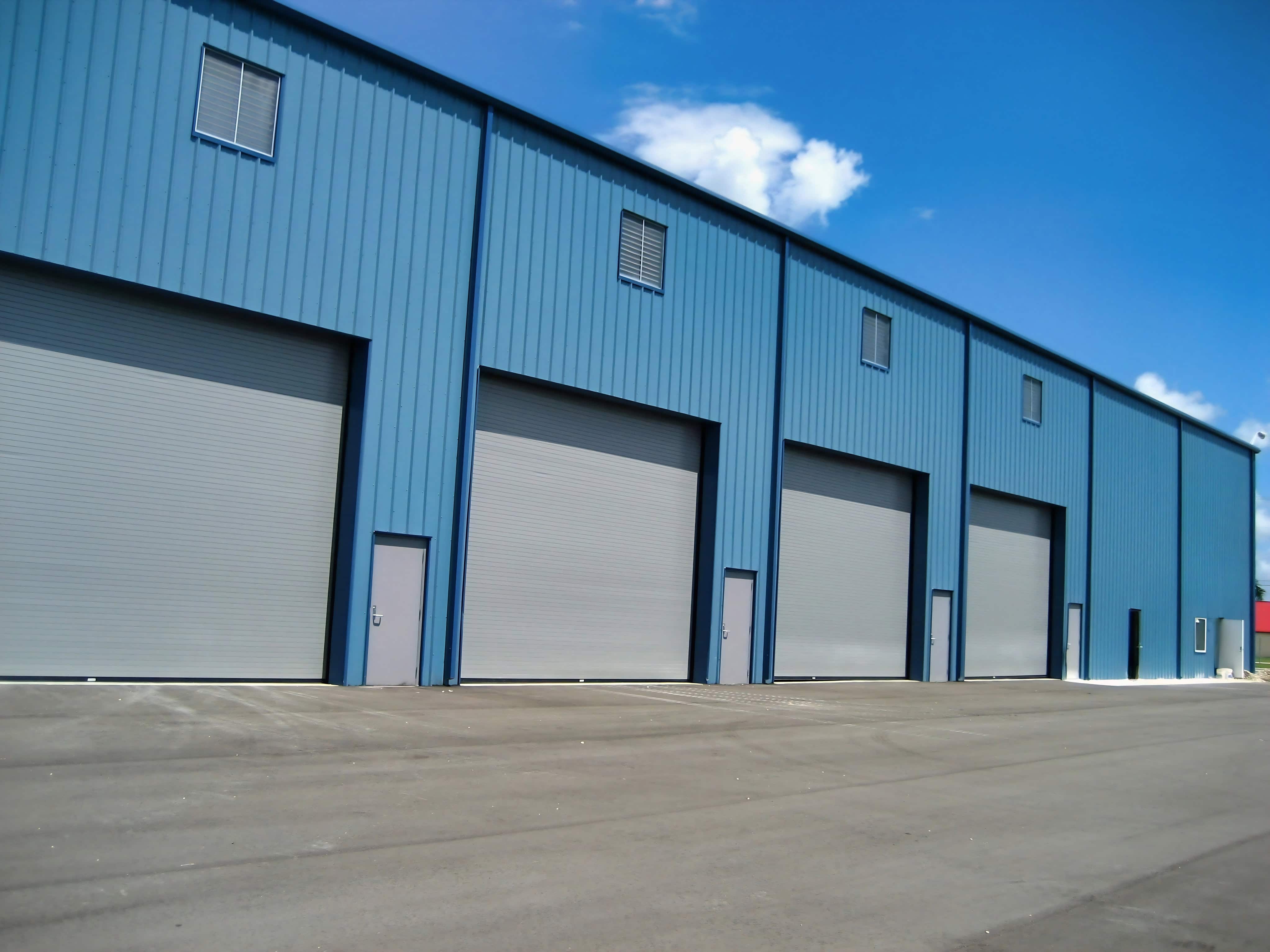
Steel Building Foundations
The steel building foundation is a crucial part of every building project, responsible for supporting the weight of the metal building as well as anchoring the metal building to the ground to meet wind load.
Steel Building Foundations
Most customers beginning a steel building project get lost in the world of the building itself and don’t give a lot of consideration to the foundation. The foundation for a commercial red-iron steel building project is complex due to the very nature of the building it supports.
Commercial Red-iron Steel Buildings transfer the majority of the weight of the building to just a handful of points (where the main frame columns are located).
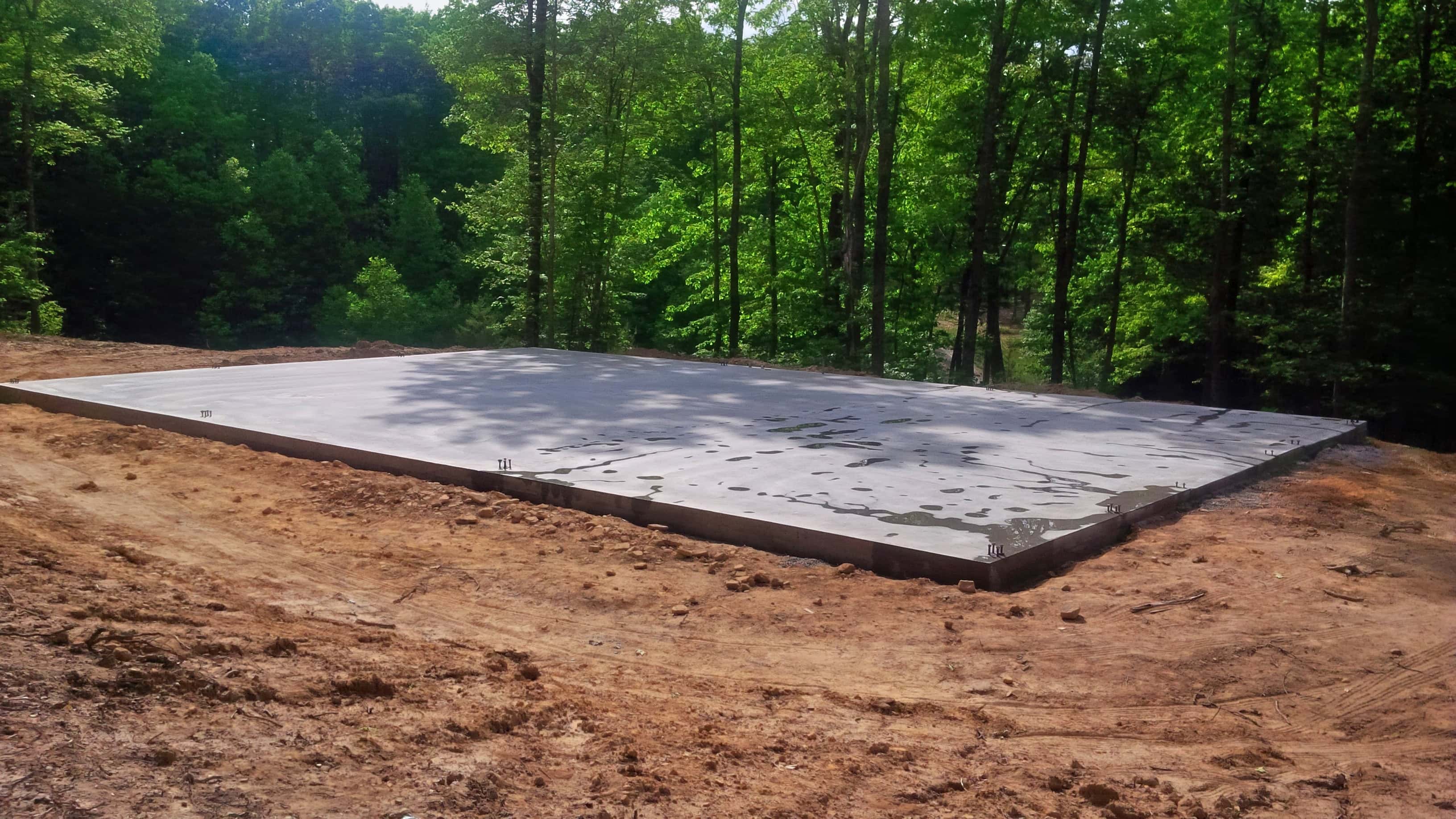
This concentration of weight requires large piers under each of the columns to support the weight of the building. The piers also support the weight of any snow on the roof (if applicable) and keep the building anchored to the ground to meet wind load requirements.
The Foundation Complexity
The slab or foundation for your steel building is more complex than customers realize. The foundation of a steel building works in conjunction with the steel building to help meet the local building codes.
Have you ever stopped to think about why mobile homes are always the first victims during extreme weather events? Sure, they are lighter than a tradition home, but the big difference is that they don’t have the benefit of a foundation to help them keep anchored to the ground.
A properly engineered foundation helps anchor the steel building to the ground and also helps the steel building transfer the energy of loads upon it into the foundation.
In order to accomplish this, steel building foundations have large piers under each of the columns of the steel building. Rebar and wire mesh are placed in the pier according to the engineer’s specifications, and hairpins wrap around the pier and extend out into the center of the slab.
The details of the piers for a steel building project are determined by the engineering of the steel building and the local codes that are to be met. There is no “one-size-fits-all” pier size: while a pier in the neighborhood of 3′ x 3′ x 20″ might be common in middle Tennessee, a pier in south Florida might be 12′ x 12′ x 4′.
It’s a valid question and the answer is simply that while anchor bolt plans specify the diameter and location of the anchor bolts used to secure the building to the foundation via it’s base plates – they specify nothing about the size of the piers under the base plates/columns.
Having the foundation for your steel building project properly engineered by a licensed engineer in your state is so important that most all counties require a copy of your stamped engineered foundation drawings be filed with the stamped engineered building drawings when you apply for a permit.
Stamped engineered foundation drawings are also needed for your concrete contractor as they provide the technical information regarding the pier size and depth as well as specific placement of rebar, wire mesh, and hairpins.
Without a set of stamped engineered foundation drawings for a project – how exactly would a concrete contractor know what he was to pour (and presumably what he was going to bid on)?
The answer is: he wouldn’t have a clue.
Concrete costs are a substantial portion of any steel building project and it’s understandable that customers want to accurately estimate this cost before committing to a project.
Here’s the problem though: in order to obtain a set of stamped engineered foundation plans for your steel building project (that you will use to solicit accurate bids from concrete contractors) the foundation engineer needs to have a set of the building engineering. Without the details provided in the building engineering, the foundation engineer can not engineer a foundation.
Here’s another problem: you don’t get a copy of the building engineering until AFTER you purchase a building. So how do you estimate concrete costs for your steel building project?
We always recommend customers talk to an experienced concrete contractor who has experience pouring slabs for steel buildings. An experienced concrete contractor will likely be able to provide you with a rough estimate of cost per sq. ft. for a finished steel building slab (including materials, labor, form, pour, finish, and anchor bolts).
The fact is that there will be costs associated with modifying the existing slab and foundation engineering will be required to determine the extent of the modifications needed.
Most customers with existing slabs have no knowledge as to what was originally poured – or when – or by whom – or if there was even any foundation engineering for the existing slab. Since the steel building foundation plays such a crucial role in supporting the steel building and helping to meet local codes, there’s no room for speculation and assumptions.
Customers with existing slabs have only two options: they can cut INTO their existing slab so that they can pour the piers as specified by the foundation engineer, OR they can pour the piers OUTSIDE of their existing slab, leaving the existing slab to become a floating floor within the building.
For customers that choose to pour piers OUTSIDE of their existing slab, a grade beam between the new piers will be required to allow use of our formed base trim to dry the building in. It’s important to note that pouring piers outside of the existing slab will result in the building being a little wider/longer than originally planned – so it’s important to make sure a larger building doesn’t create setback or other code compliance issues.
The Buck Steel Advantage
Whether you are considering a 40′ x 60′ metal garage, a 10,000 sq. ft. steel warehouse, a 3,000 sq. ft. steel airplane hangar, a 30,000 sq. ft. open steel riding arena, or a new steel church for your congregation, a steel building project can sometimes be intimidating to navigate alone. Whether for personal or business use, you want to minimize the cost of your steel building project while maximizing the benefit it provides.
Why not give yourself The Buck Steel Advantage and have a reputable metal building supplier, serving the steel building customer for nearly 20 years, with 1,000’s of completed projects, guide you through the metal building process?
Getting started is easy with Buck Steel
Request A Quote Today or Call (866) 574-2825 to speak to a member of our team.
Comments, Questions and Answers
Hi I need a foundation plan for the building departmant in Eatonville, WA zip 98328. I already orded the building and it is 40’x 80′ x16′ tall. Can you help me with a monlithic design and do it in a few days?
Thank you for reaching out to us. We only provide foundation engineering services for our steel building customers. You should be able to do an internet search on “structural engineer washington state” and find someone to help you. The structural engineer will require a copy of the stamped building plans so they can review the column reactions. Structural engineers have different work loads and schedules, we generally take 10-14 days to get a set of foundation plans completed for a basic foundation. Good luck!