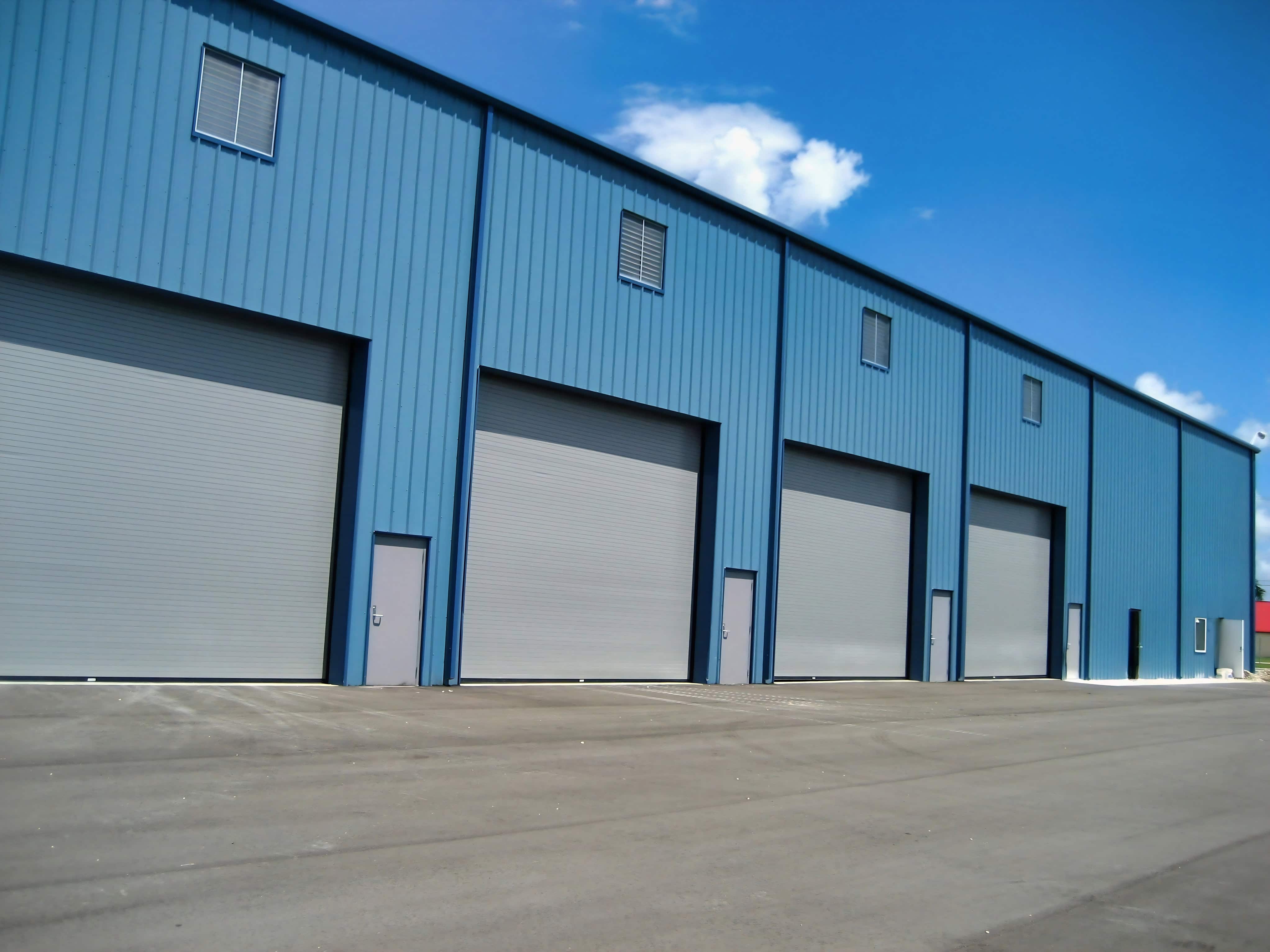
Steel Buildings for RV Storage
With both the popularity and cost of RV’s on the rise, a metal building is the perfect solution to storing and protecting your RV investment.
As much as you would probably like to — you will not be on the road with your RV 12 months out of the year. There are likely to be prolonged periods of time that it will be parked, especially if you tend to reduce your trips during the long winter months.
Your RV is a substantial investment, and leaving it unprotected outdoors is probably going to leave you feeling uncomfortable. Renting indoor storage is an option, but the availability of such facilities is limited and even when they are available, they can be expensive.
Many RV owners decide to purchase a steel building and store their own RV where they can keep an eye on it themselves. Steel buildings for RV storage are very affordable, when compared to traditional methods of construction, easy to erect, and require very little in the way of maintenance.
OK, sounds great, so where do you start? Here are some helpful tips to help guide you in the right direction.
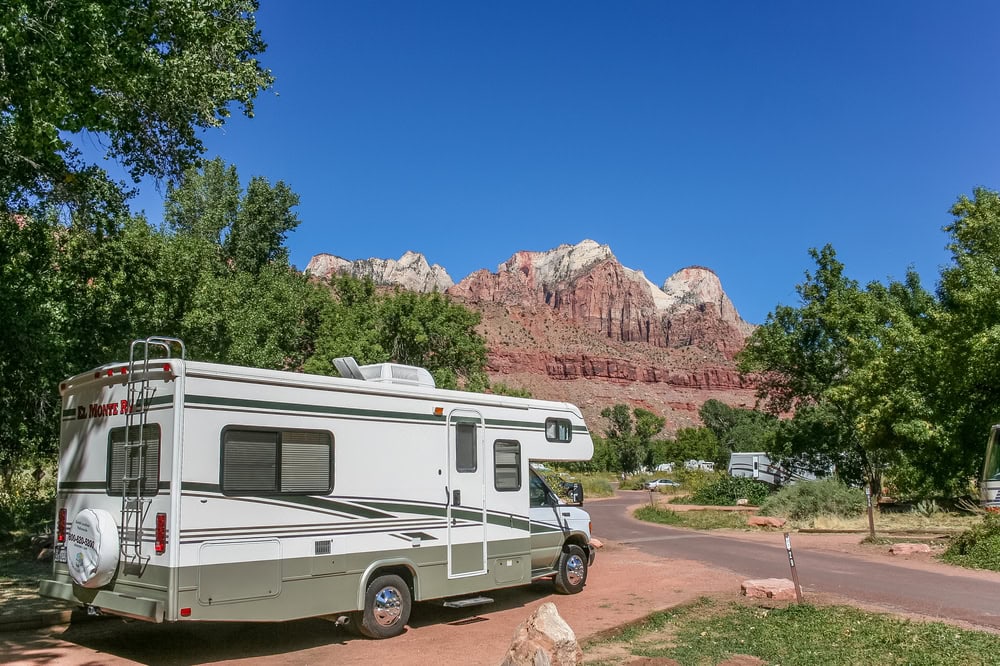
Can you put a steel building on your property?
This simple question is often overlooked and a quick visit to your county’s building department and a call to your HOA (if you live in one) is all it takes to find out. As your building will be designed for an RV, it’s likely to be tall – with a minimum of a 14′ or 16′ eave height – make sure there are no height restrictions imposed by your building department or HOA, as well as restrictions on the use of steel wall panels.
What size is best?
Of course, the size of your RV will dictate the answer to this question – but rollup door size has a big influence as well. For most RV owners, a rollup door of 12′ x 14′ is the minimum to be considered, with many opting for a 14’ x 14’ or 14’ x 16’ door.
Keep in mind 2’ of space is needed above the rollup door for when the door is up so rollup door height has a direct influence on the eave height of the building. For example, a 14’ high door will require a minimum 16’ eave height and a 16’ door will require a minimum 18’ eave height.
When considering the height of your steel building, don’t’ forget to take into consideration having ample room to get on the top of your RV for maintenance when it’s inside!
Is Insulation Needed?
Insulation is an often overlooked component of any steel building purchase. Generally speaking, roof insulation is very important in helping to address condensation issues and should be included.
Standard white vinyl backed fiberglass insulation is relatively inexpensive and trying to save a few dollars by not insulating the roof of your steel building will likely result in condensation forming on the inside of the roof panels – especially during the warmer summer months. Wall insulation is less important, but certainly something to consider if you plan on spending time inside the building or plan on climate controlling the space.
Insulation options for steel buildings range on the low-end from R10 / 3″ insulation all the way up to to R76 Simple Saver System insulation.
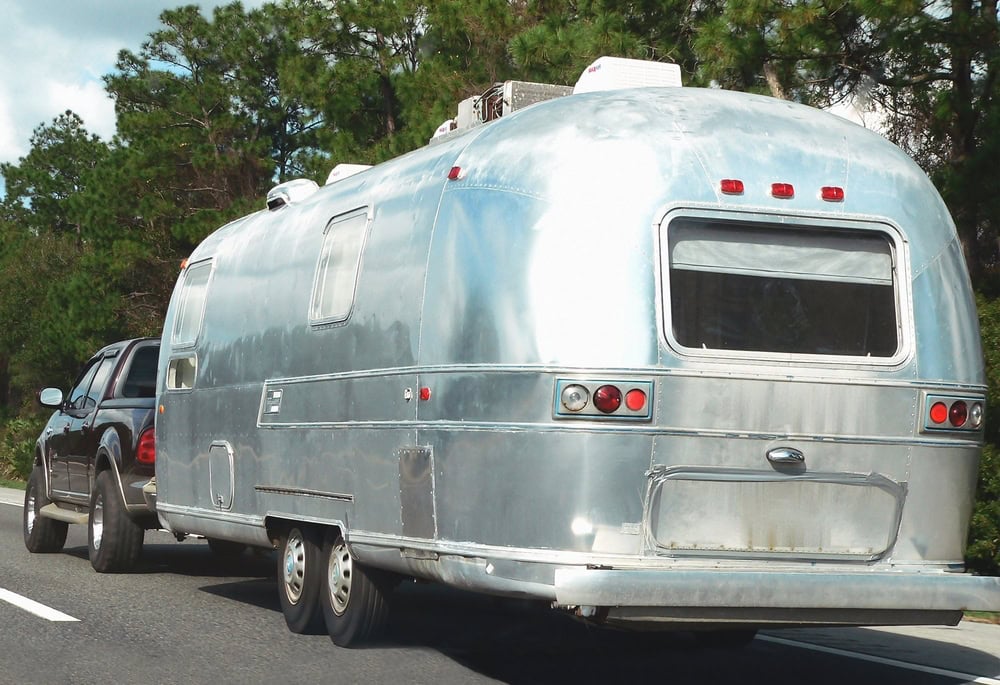
How Important is Ventilation?
If the building is going to be regularly accessed, ventilation is probably not needed. However, if your RV is going to sit in the building for prolonged periods without anyone accessing the space to introduce even temporary air flow, then ventilation is a good idea.
A standard ridge vent is a good way to get warmer air at the peak of the roof out of the building. A quality ridge vent will contain systems for preventing rodents and rain water from entering the building as well as have an adjustable damper.
Unlike residential housing where fresh air enters the eave and flows up to the ridge vent creating a circular motion of air flow, steel buildings do not have eaves. An easy way to address this is to place a fixed louvered vent in the gable end of the building which will allow fresh air to flow into the building and then up and out through the ridge vent.
What Other Costs Are Involved?
There are namely two additional costs involved in building a steel building for RV storage – namely the cost of pouring a slab for the building and the labor to erect the building.
The cost of concrete can be broken down into two parts: first, the foundation engineer who designs the slab and second, the concrete contractor who forms, pours, and finishes the slab. The cost of concrete varies a great deal from region to region but an experience local concrete contractor should be able to provide you with a per square foot estimate for a monolithic pour for a steel building project.
The cost of erecting labor also varies greatly from region to region. When selecting an erecting crew, it’s important to select a crew with steel building experience, that is licensed, insured, and has some factory training. You don’t want to hire a crew that is going to damage the building you just purchased! For budgeting purposes and for smaller buildings, the costs of concrete and erecting should roughly be equal to the cost of the building itself.
The Buck Steel Advantage
Whether you are considering a 40′ x 60′ metal garage, a 10,000 sq. ft. steel warehouse, a 3,000 sq. ft. airplane hangar, a 30,000 sq. ft. open steel riding arena, or a new steel church for your congregation, a steel building project can sometimes be intimidating to navigate alone. Whether for personal or business use, you want to minimize the cost of your steel building project while maximizing the benefit it provides.
Why not give yourself The Buck Steel Advantage and have a reputable metal building supplier, serving the steel building customer for nearly 20 years, with 1,000’s of completed projects guide you through the metal building process?
Request A Quote Today or Call (866) 574-2825 to speak to a member of our team.
We welcome your comments and questions!